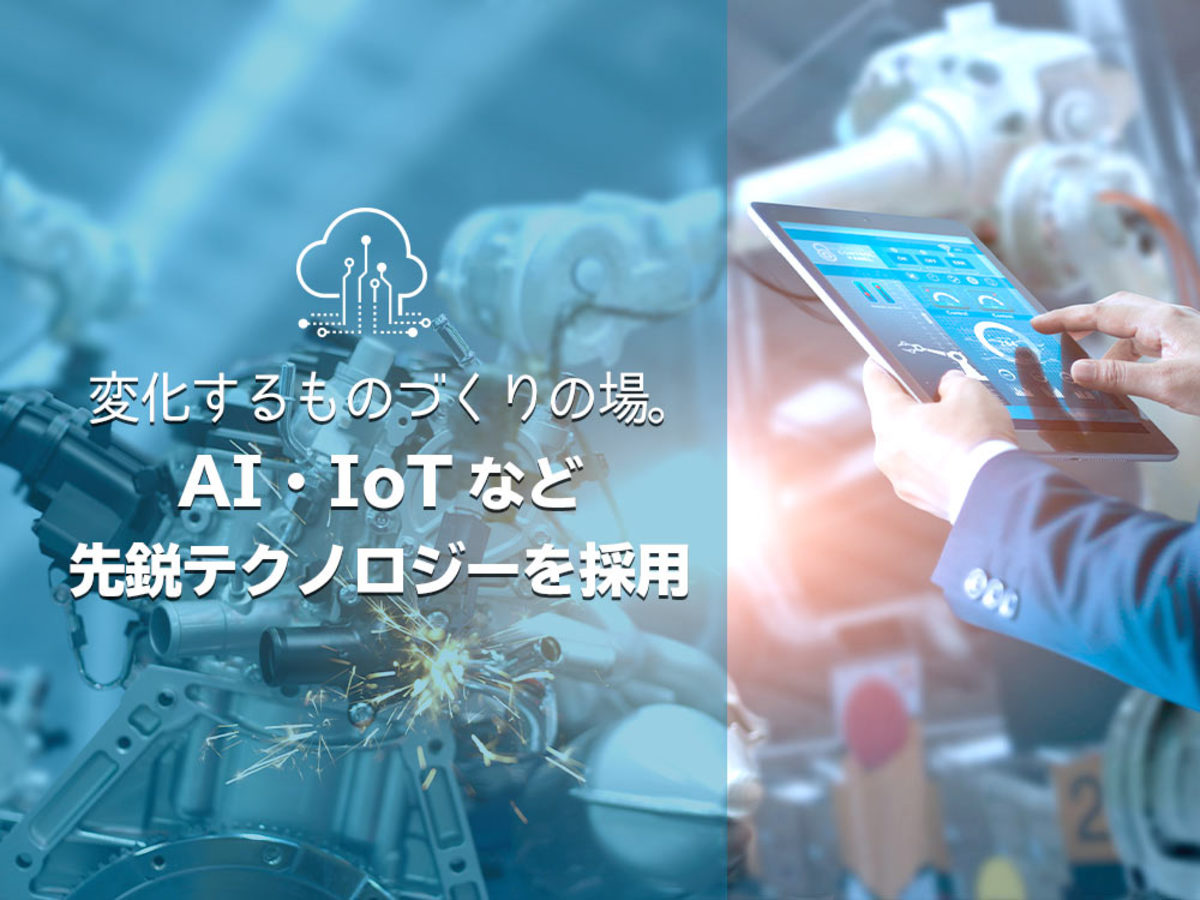
「スマートファクトリー」とは?ものづくりのプロセスに新たな付加価値を!
スマートファクトリーという言葉をご存知ですか?簡単に言うと「スマートフォン」「スマート家電」などと同じく、AI・IoTなど先鋭テクノロジーを採用した「スマートな(賢い)工場」といった意味合いの言葉です。
あらゆる製造工程をデジタル化、数値化、見える化して生産性向上を実現。しかもそれだけに留まらず、工場そのものに新たな付加価値をプラスし、新たなソリューションを生み出す可能性も秘めています。この記事では、ビジネスパーソンに向けて「スマートファクトリーとは何か?」「そのメリットとは?」という点を紐解き、日本国内の導入事例も交えつつ、分かりやすくお伝えします。
スマートファクトリーとは?
*スマートファクトリーとは、ものづくりをする工場ラインでデジタルデータをフル活用する仕組みのことです。*ものづくりの現場でも、各プロセスから徹底的に数値データを取得してPDCAを回す。PDCAを回すことにより、業務プロセスの改善や、品質・生産性の向上を実現する工場のことです。
具体的にどうやって、ものづくりのプロセスから細かな数値データを取得するのでしょうか?
それは、AIやIoTの活用です。これらの先進技術を活用して、ものづくりのプロセスを大きく変革させようという取り組みです。
参考:
スマートファクトリーとは | 製造業のAI×IoT化事例・課題と成功の秘訣を解説|Ledge.ai
「 スマートファクトリーロードマップ 」〜 第4次産業⾰命に対応したものづくりの実現に向けて 〜|経済産業省 中部経済産業局
スマートファクトリーの概念が提唱されている背景
この、スマートファクトリーという概念は、どういった背景で登場したのでしょうか。
ドイツ発祥の第4次産業革命「インダストリー4.0」
スマートファクトリーが注目されるきっかけとなったのは、*ドイツ政府による「インダストリー4.0」という産学連携の国家プロジェクト。*AIやIoTなどの最先端技術の進化とともに、ものづくりのICT化を推進しようという考え方です。これは、第4次産業革命とも言われ、産業構造の変革が起こる、と期待を集めています。
インダストリー4.0で目指すものは、スマートファクトリーを中心としたエコシステムの構築です。人間も、機械も、その他の工場内プロセスも、互いに通信することで「各製品がいつ製造されたか」「どこに納品されるべきか」といった情報を共有し合うことを目指します。
この仕組みにより、製造プロセスをより円滑にし、さらには、既に自社が持っている強みのさらなる進化や、新たなビジネスモデルの構築に繋げることを目的としています。「もの」そのものを作り出す価値から、工場ラインの「サービス」「ソリューション」を進化させて新たな付加価値を生み出す。つまり、現場力の向上を後押しする取り組みとも言えます。
この潮流を受け、日本政府もスマートファクトリー構想を推進するための支援戦略「コネクテッドインダストリーズ」を打ち出しました。
経済産業省の調べによると、製造過程のデータ化・自動化の実施については、「可能であれば実施したい」という割合が増加しています。(※2019年時点)
しかし、「実施している」または「実施する計画がある」と答えた割合は、そう多くはありません。デジタル化の必要性は感じているものの、実行まで移せている企業はまだ少ないと考えられます。
参考:総務省|平成30年版 情報通信白書|インダストリー4.0とは
スマートファクトリーのメリット
工場内プロセスにおけるデジタルデータの活用により、以下のような効果が期待できます。
①品質の向上
####(1)不良率の低減
*従業員の作業内容(作業⼿順、作業結果など)をセンシング(センサーなどで計測・数値化)することで、作業内容を収集・把握できます。*ポカミスが発⽣した際には、すばやく従業員へ通知。また、過去のポカミスを分析することで、ポカミスが発⽣しやすい作業⼯程を特定できます。分析結果に基づいて、従業員を育成したり、設計を変更することで、ポカミスの発⽣を抑制し、不良率を削減・最⼩化できます。
(2)品質の安定化・ばらつきの低減
設備にセンサーを取り付けてモニタリングをします。これにより、加⼯⼨法など製品の品質データと、設備側の加⼯条件・設定値を収集・把握します。蓄積したデータを分析し、品質のばらつきの要因を特定できれば、加⼯誤差や加⼯性能の改善につながる加⼯条件・設定値をモデル化できます。
また、各従業員の作業状況(作業動線、作業時間、作業内容など)をセンシングし、データ収集する方法も想定できます。こうして収集したデータを分析し、作業のばらつきの要因を特定することで、作業の改善につながる作業条件をモデル化できます。
(3)設計品質の向上
出荷する製品にセンサーや通信機能を搭載することで、ユーザーの手元に届いてからの製品の使⽤状況や使⽤環境のデータを収集・把握できます。収集したデータと設計データとを関連付けて因果関係を明らかにすることで、品質・信頼性の向上につながる設計仕様・⽣産⽅法を分析。
この分析結果に基づいて、設計仕様・⽣産⽅法を修正・改善して最適化することで、製品の品質・信頼性向上につながります。
② コスト削減
(1)材料の使用量の削減
過去の設計事例の分析や、 解析・シミュレーションソフトなどによって、材料の軽量化や部品点数の削減につながる形状・構造等を知⾒として蓄積し、モデル化。設計改善モデルを構築できれば、材料の使⽤量を最⼩化できます。
(2)生産リソースの削減
「MES(製造実⾏システム)」 などのデータを利⽤します。作業プロセスの進捗状況や、ヒト(⼯数)、材料、 エネルギーの投⼊状況を収集・ 把握。 ⽣産の作業プロセスの進捗状況を踏まえて、ヒト(⼯数)、材料、エネルギーの予定投⼊量、予定⽣産量などを予測。この予測をもとに計画を修正・最適化することで、 投⼊するヒト(⼯数)、材料、 エネルギーを最⼩化できます。
(3)在庫削減
「MES(製造実⾏システム)」などのデータを利⽤することで、⽣産計画や⽣産実績データの⼊⼒・表⽰・確認が簡単になります。受注、⽣産、出荷の計画・ 実績データを連動させて分析することで、需給変動要因を明らかにしたり、需給を予測。予測に基づいて、調達した資材や、⽣産した製品の在庫が最⼩化となるよう、 ⽣産計画・出荷計画の作成を⾃動化・最適化できます。
(4)設備の管理・状況把握の省⼒化
設備にセンサーを取り付けてモニタリングをします。
設備の設置場所にいなくても、複数設備の稼働状況を、遠隔でリアルタイムに収集・監視。
設備に異常などが発⽣したときに、従業員への通知を⾃動化することで、監視・ 点検の管理⼯数を最⼩化できます。
③生産性の向上
(1)設備・ヒトの稼働率の向上
「MES(製造実⾏システム)」などのデータを利⽤し、 ⽣産ライン全体の設備の稼働・ヒトの作業の進捗状況を収集・把握できます。自動でデータ取得した稼働・進捗状況をもとに、各プロセスの完了予定時間を予測。⽣産ライン全体の⽣産完了予定時間が最短化されるよう、段取り替えをすることで、設備・ヒトの⾮稼動時間の最⼩化につながります。
(2)ヒトの作業の効率化、作業の削減・負担軽減
「モバイル端末」「スマートグラス」などを活⽤します。調達した資材や⽣産した製品の管理情報、 ⽣産情報、設備の稼動情報を迅速かつ簡易に⼊⼒・ 表⽰できます。作業の進捗状況に応じて、 手元のデバイスに必要な情報や作業指⽰を予測して表⽰。情報の⼊⼒・表⽰の⾃動化による作業の短時間化や、 適切な判断を⽀援し、作業プロセスを効率化できます。
また、設備にセンサーを取り付けたり、 ヒトの作業状況(作業動線、 作業時間、作業内容など)をセンシングすることで、稼働状況・作業状況を収集・把握します。収集したデータをロボットに学習させ、ヒトの⾏動を予測し、ロボットとヒトが協業できるようになれば、ヒトの作業効率を向上できます。
(3)設備の故障に伴う 稼動停⽌の削減
設備にセンサーを取り付けて、稼働状況を収集・監視。 集めたデータと設備異常とを関連付けて、設備の故障につながる兆候・条件を明らかにすることで、故障の発⽣時期を予測できます。
*この予測に基づき予防保全することで、故障の発⽣を抑制。*想定外の稼動停⽌時間を削減・ 最⼩化できます。
また、ヒトへのすばやい通知にもつながります。過去の故障事例を分析することで、正確な原因究明や適切な対策の⽴案につながります。
④製品化・量産化の期間短縮
(1)製品の開発・ 設計の⾃動化
設計事例をデータベースとして蓄積しておけば、過去の事例を容易に参照できるようになります。解析・シミュレーションソフトを利⽤すれば、構造などを解析できます。設計仕様を満たし、かつ、⽣産しやすい形状・構造等を知⾒としてモデル化。構築した設計改善モデルを⽤いて、製品設計を⾃動化することで、製品開発・設計期間を短縮できます。
(2)仕様変更への 対応の迅速化
「E-BOM(設計部品表)」や「M-BOM(製造部品表)」などを利⽤すれば、部品の詳細情報を簡単に表⽰・確認できます。E-BOMやM-BOMをデータ連携することで、開発、 設計、⽣産のデータを⼀元管理。もし仕様変更となった場合、影響範囲を事前に分析でき、仕様変更の対応時間を最⼩化できます。
(3)⽣産ラインの設計・ 構築の短縮化
「⽣産ラインシミュレーター」を利⽤し、パソコン上で⽣産ラインを設計。
⽣産ラインのレイアウト、⽣産能⼒、作業⼯程、搬送ルート、投資コストなどを事前に評価・検証できるようになります。⽣産現場へ実装することで、構築時の試⾏錯誤を削減。⽣産ライン 構築期間を短縮できます。
⑤⼈材不⾜・育成への対応
(1)多様な⼈材の活⽤
各従業員の作業熟練度、 知識、⾝体能⼒、使⽤⾔語などを、データベースとして蓄積。
各従業員の特性情報を利⽤できます。 ヘッドマウントディスプレイや、⾳声認識などのウェアラブルデバイス、 パワーアシストスーツ、⽣体センサーなどを活⽤し、ヒトの能⼒を拡⼤することで、特性が異なる多様な⼈材を活⽤できるようになります。
(2)技能の継承
熟練技能者の技能(段取り 調整⼒、状況判断⼒、 ⼿わざ、トラブル対応⼒など) をセンシングし、データベースとして蓄積します。収集したデータを分析し、 熟練技能者が優れている点を明らかにすることで、技能・ ノウハウ・知⾒を体系化。体系化した技能・ノウハウ・ 知⾒を国内外の拠点へ共有することで、技術継承し、ヒトの能⼒を向上できます。また、それらをスマートロボットに学習させることで、ヒトを代替できるようになります。
⑥新たな付加価値の提供・提供価値の向上
(1)個別ニーズに合わせた多品種の製品の提供
各製品に共通する部分を定義して、製品の構造、 設計・⽣産プロセス、加⼯基準などを共通化。設備・ヒトへの作業指⽰・ 部品供給や段取り替えを⾃動化・効率化することで、多品種の製品をフレキシブルに⽣産できるようになります。
(2)顧客ニーズに合わせたオン デマンドな製品・ サービスの提供
「ERP(統合業務管理システム)」「MES(製造実⾏システム)」「SCM(サプライチェーン マネジメントシステム)」などのデータを活用します。受注、 調達、⽣産、物流、販売 などの計画・実績データを、 簡単に表⽰・確認。そのデータを分析することで、需要を予測できます。社内関係部⾨やサプライチェーン全体で、 ⽣産計画・物流計画を最適化することで、顧客ニーズに合わせてオンデマンドに製品・サービスを提供できるようになります。
(3)提供可能な加⼯技術の拡⼤
「MES(製造実⾏システム) 」などのデータを活用します。⽣産の進捗状況を収集・ 把握し、共同受注を⾏う企業間で データ連携。各企業における加⼯時間・ 加⼯ロット単位などの違いを考慮して、全体で⽣産計画・物流計画などを最適化することで、共同受注⽣産体制を構築し、様々な加⼯技術を提供できるようになります。
(4)新たな製品を先回りした企画・提案
出荷する製品にセンサーや通信機能を搭載します。その後の製品の使⽤状況や、使⽤環境のデータを収集・把握できるようになります。このデータを分析し、 ユーザを⾏動観察する (⼈間⼯学、⼼理学などの観点から分析する)ことで、 ⾮顕在ニーズを把握。先回りして製品・機能・サービスを企画・提案することも可能になります。
(5)製品に関連した新たな サービスの提供
出荷後の製品の使用状況をデータで把握することは、製品改善につながるインサイトや、別⽤途への製品利用実態など、新たなインサイトを獲得できます。製品に関連した新たなサービス・アフター サービスの提供につながっていきます。
(6)製品性能 の最⼤化・ カスタマイズ化
出荷する製品にセンサー・通信機能を搭載することで、製品の使⽤状況、 使⽤環境のデータ、製品の制御データを収集・把握できます。このデータを分析すれば、ユーザの手元での製品使⽤⽅法の傾向を把握できます。 使⽤⽅法の傾向に合わせて、製品の制御設定値を最適化することで、製品の性能を最⼤化・カスタマイズ化できます。
(7)製品への新規機能の追加
製品に通信機能を搭載し、この通信機能を通じてソフトウェアを遠隔アップデートすることで、製品に新規機能を追加できるようになります。
参考:「 スマートファクトリーロードマップ 」〜 第4次産業⾰命に対応したものづくりの実現に向けて 〜|経済産業省 中部経済産業局
スマートファクトリーの事例
ここからは、実際にスマートファクトリーの仕組みを導入している企業事例を紹介します。
株式会社ダイセル(大手化学品メーカー)
株式会社ダイセルは、エアバッグの基幹部品の製造を手掛ける会社として知られています。
ここでは、「画像解析」により作業員の逸脱動作や設備・材料の不具合などの異常を早期に発見。現場管理監督者が事故を未然に防止できる環境を実現しました。
この「画像解析システム」は、「ヒト」に対応する人物動作解析、「設備」に対応する設備異常解析、「材料」に対応する溶接異常解析で構成。
人物動作解析では、3次元形状を取得できるカメラを用いて作業者の手やひじ、肩などの関節位置情報を取得。標準動作モデルと関節位置情報を統計的に比較することで逸脱動作を検知します。「両手」「目視」「屈み」の3項目について、規定したしきい値を超えると、生産ラインの監督者に通知が送られる仕組みです。
同じ仕組みを、設備や材料監視にも活用。通常画像との差分を分析することで、異常を検知しています。例えば溶接の場合なら、カメラが溶接の様子とその過程で生じる光の波長データを常時収録。グラフ化した発光データに通常と違う偏りがあれば異常と検知されます。
さらに万が一、生産工程に不適切な作業が発見された時は、シリアル単位で最終製品を追跡できるトレーサビリティも実現しました。
ダイキン工業株式会社(総合空調)
空調機・化学製品などの製造で知られるダイキン工業株式会社。
ここでも、「画像解析システム」を活用し、空調機の製造に欠かせない熟練ノウハウのデジタル化に着手。スマートファクトリーの導入により、技能の底上げとグローバル人財育成に向けた取り組みを進めています。
空調機には図面だけでは表せない複雑な内部構造があり、組立工程の中には技術者の感覚に頼る部分がまだまだ残っています。
こうした製品をグローバルかつスピーディーに展開していくには技能伝承と訓練の効率化が重要です。
先述した株式会社ダイセルに導入した「画像解析システム(※日立との協業によるもの)」を応用し、熟練技術者が持つノウハウのデジタル化を実現。技術の継承、人材育成に役立てています。
オークマ株式会社(工作機械)
オークマ株式会社では、工作機械の製造を手掛けています。超多品種少量の生産でも、大量生産並みの高い生産性を実現する「マスカスタマイゼーション」に向けた取り組みを導入しています。
ロボットなどを高度に活用し、自動化・無人化を推進。従来は、適用が難しいとされた多品種少量生産の重量部品の加工においても、ロボットを活用することで、生産性向上を実現させました。
JUKIグループ(工業用ミシン / 産業装置 / 家庭用ミシン他)
JUKIグループはミシン製造のほか、産業装置の製造を幅広く手掛け、プリント基板生産における高度なプロダクトでも強みを持っています。
IoTで部品や設備をつなぎ、生産ラインの上流から下流までをトータルに一元管理する新たなデジタルソリューションを作り出しました。生産ラインで課題となっていた生産工程の可視化を解決。
「Sense(見える化)」→「Think(分析)」→「Act(対策)」のサイクルを循環させながら、「生産進捗・実績管理」「稼働実績分析」「不具合解析」「設備保全」「在庫管理」といった従来ボトルネックになっていた部分を改善し、生産性向上や不具合発生時の原因解析率向上を実現しました。
これにより、導入1カ月で生産性が約30%も向上につながりました。
TOTO滋賀⼯場(住宅設備機器の成形・組み立て)
TOTO滋賀⼯場では、⼤型投資で最新鋭の技術をつぎ込み、国内外全ての⼯場のモデルとなる先端の製造現場を作り上げました。
導入したプロセスは「生産」、スマート化の主目的は「従業員による作業の効率化、作業の削減・負担軽減」です。
ラインを流れる衛⽣陶器は1個1個、品番が異なる混流⽣産です。貼り合わせる位置も毎回違ってきます。そんな中でも、ロボットは最新のセンサー技術を使い、⼨分の狂いもなく貼り合わせ位置の違いを正確に識別。かつ迅速に位置を合わせられるように プログラミングされています。
また、陶器に釉薬(ゆうやく)を吹き付ける「施釉(せゆう)」という作業⼯程を3台のロボットを同時並行でに動作させることに置き換えました。
薬を吹き付けるロボットが、配置された衛⽣陶器の型番に応じたプログラムをそのつど読み込んで施釉作業を実⾏します。
また、パレットにICタグなどを組み込んでおり、衛⽣陶器に貼り付けたバーコードにひも付けて、⼀元管理。この ICタグなどを読み取れば、パレット番号も固有の製品のバーコードも分かります。バーコードから、品番や⼯程で発⽣する各種ログ情報を呼び出すことができ、その項⽬数は475項⽬にも及びます。これを製造ビッグデータとして⼯程管理や品質管理、出荷後のトレーサビリティーなどに活⽤しています。
参考:スマートファクトリー①日立が提案するスマートファクトリーと協創事例|日立
「 スマートファクトリーロードマップ 」〜 第4次産業⾰命に対応したものづくりの実現に向けて 〜|経済産業省 中部経済産業局
スマートファクトリーは、「モノ」生産プロセスに新たな付加価値をプラスしてくれる概念
事例で述べたように、国内大手製造関連企業ををはじめとして、少しずつスマートファクトリーの導入が進みつつあります。デジタルデータの活用によって進歩する部分は、生産性向上のような、純粋に「モノ」を生産するプロセスだけに限りません。
*人材不足の解消、熟練工の技術の継承、さらには、出荷後のトレーサビリティーなどによって、新たな付加価値の提供にもつながります。*スマートファクトリーという概念の出現により、工場とはもはや、「モノ」を作って出荷するだけの役割ではなくなってきたと言えるでしょう。
関連記事
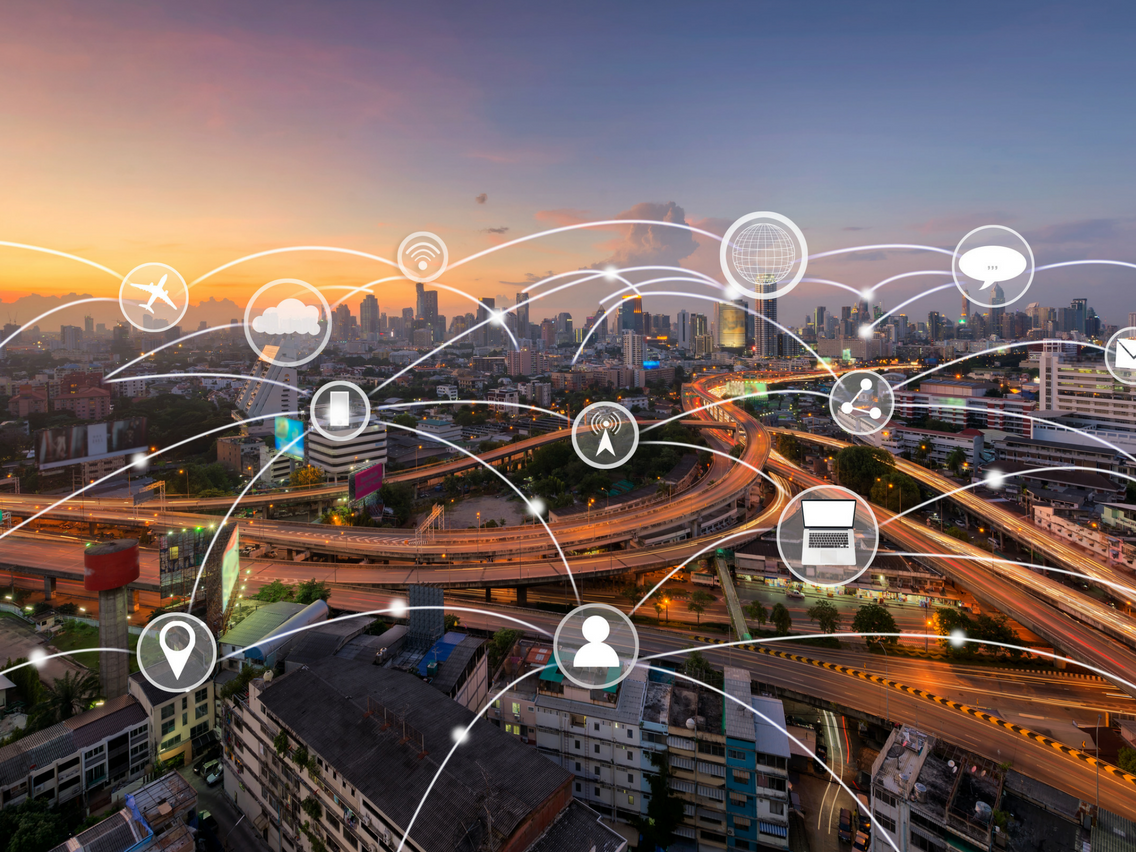
日本はデジタル技術にどう向き合う?「コネクテッド・インダストリーズ」の基本を解説
ほとんど毎日のように、IoTやAIに関するニュースを目にするようになりました。日本全体としてデジタル技術をどのように発展させ、経済成長につなげていこうとしているかを俯瞰的に説明できる方は少ないのではないでしょうか。日本政府は、国内のデジタル技術を全面的に支援するために「*コネクテッド・インダストリーズ*」という政策を掲げています。今回は、コネクテッド・インダストリーズの基本概念を解説します。
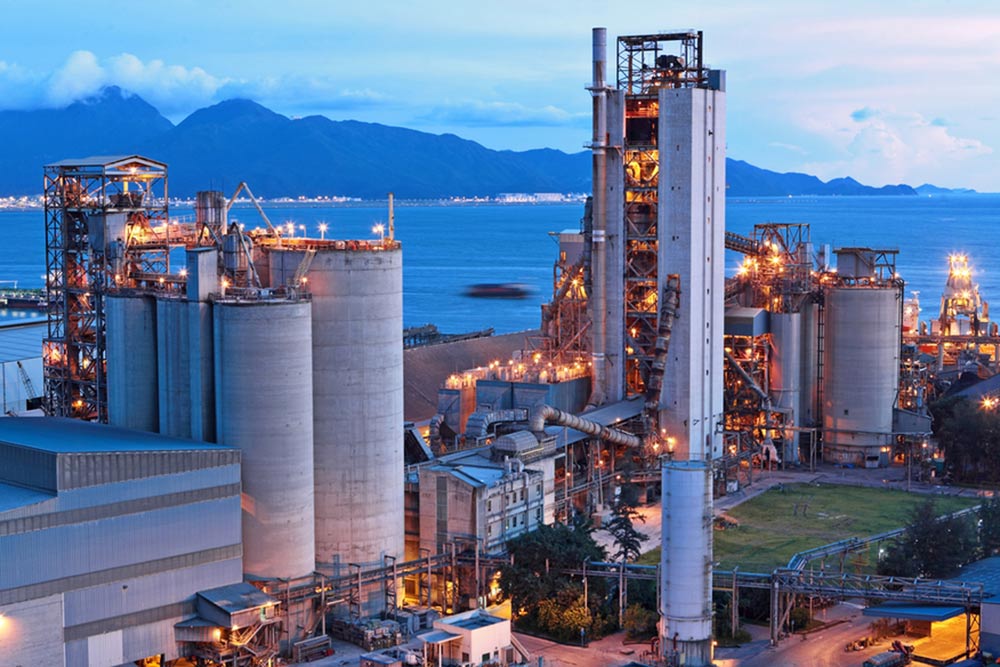
ドイツ発の産業革命「インダストリー4.0」とは?事例や企業が把握すべきポイントを解説
インダストリー4.0とは、官民一体となって取り組み、生産プロセスをデジタル化することによって大幅な業務改善を行う2011年にドイツにて立ち上がったプロジェクトです。今回は、インダストリー4.0について基礎知識から企業が把握すべきポイント・問題点まで、事例を交えながら解説していきます。
- PDCA
- PDCAとは、事業活動などを継続して改善していくためのマネジメントサイクルの一種で、Plan,Do,Check,Actionの頭文字をとったものです。
- デバイス
- デバイスとは「特定の機能を持つ道具」を表す語で、転じてパソコンを構成するさまざまな機器や装置、パーツを指すようになりました。基本的に、コンピューターの内部装置や周辺機器などは、すべて「デバイス」と呼ばれます。
- データベース
- データベースとは、複数のアプリケーションまたはユーザーによって共有されるデータの集合体のことです。特定のテーマに沿ったデータを集めて管理され、検索や抽出が簡単にできるようになっているものを指します。
- レイアウト
- レイアウトとは、もともと「配置」や「配列」を指す語です。ここでは、「ホームページレイアウト(ウェブレイアウト)」と呼ばれる、ホームページにおけるレイアウトについて説明します。
- データベース
- データベースとは、複数のアプリケーションまたはユーザーによって共有されるデータの集合体のことです。特定のテーマに沿ったデータを集めて管理され、検索や抽出が簡単にできるようになっているものを指します。
- ディスプレイ
- ディスプレイ(display)とは、文字や図形を表示する装置のことを言います。 テレビと同じ原理のCRTディスプレイや、設置面積が小さく消費電力の少ない液晶ディスプレイや、ガス放電を利用したプラズマディスプレイなど、種類も多くあります。
- ウェアラブルデバイス
- ウェアラブルデバイスとは、手首や腕、頭など体の一部に装着して使用するコンピュータデバイスのことを指します。Googleの開発しているGoogleGlassやサムスンのGalaxyGear、AppleのAppleWatchなどがあります。メガネや腕時計のような形で身に付けることができ、スマートフォンにかわる端末として注目されています。
- データベース
- データベースとは、複数のアプリケーションまたはユーザーによって共有されるデータの集合体のことです。特定のテーマに沿ったデータを集めて管理され、検索や抽出が簡単にできるようになっているものを指します。
- サイクル
- サイクルとは、スタートしてゴール、そしてまたスタートと、グルグルと循環して機能する状態のことを言います。まわりまわって巡っていく、といった循環機構をさすことが多いです。水の循環サイクルというように、実は繰り返しになってしまう使われ方もすることもしばし。また、自転車に関する事柄として、サイクルスポーツなどという使われ方をされることもあります。
- タグ
- タグとは、原義では「モノを分類するために付ける小さな札」のことです。英語の「tag」を意味するものであり、荷札、付箋といった意味を持っています。特にインターネットに関する用語としてのタグは、本文以外の情報を付与するときに用いられます。
- ビッグデータ
- ビッグデータとは、一般に、インターネットの普及とITの進化によって生まれた、事業に役立つ知見を導くためのデータのことを指します。「データの多量性」だけでなく、「多様性」があるデータを指します。
おすすめ記事
おすすめエントリー
同じカテゴリから記事を探す
カテゴリから記事をさがす
●Webマーケティング手法
- SEO(検索エンジン最適化)
- Web広告・広告効果測定
- SNSマーケティング
- 動画マーケティング
- メールマーケティング
- コンテンツマーケティング
- BtoBマーケティング
- リサーチ・市場調査
- 広報・PR
- アフィリエイト広告・ASP
●ステップ
●ツール・素材
- CMS・サイト制作
- フォーム作成
- LP制作・LPO
- ABテスト・EFO・CRO
- Web接客・チャットボット
- 動画・映像制作
- アクセス解析
- マーケティングオートメーション(MA)
- メールマーケティング
- データ分析・BI
- CRM(顧客管理)
- SFA(商談管理)
- Web会議
- 営業支援
- EC・通販・ネットショップ
- 口コミ分析・ソーシャルリスニング
- フォント
- 素材サイト
●目的・施策
- Google広告
- Facebook広告
- Twitter広告
- Instagram広告
- LINE運用
- LINE広告
- YouTube運用
- YouTube広告
- TikTok広告
- テレビCM
- サイト制作・サイトリニューアル
- LP制作・LPO
- UI
- UX
- オウンドメディア運営
- 記事制作・ライティング
- コピーライティング
- ホワイトペーパー制作
- デザイン
- セミナー・展示会
- 動画・映像制作
- データ分析・BI
- EC・通販・ネットショップ
- 口コミ分析・ソーシャルリスニング
●課題
●その他
